you have climbing equipment
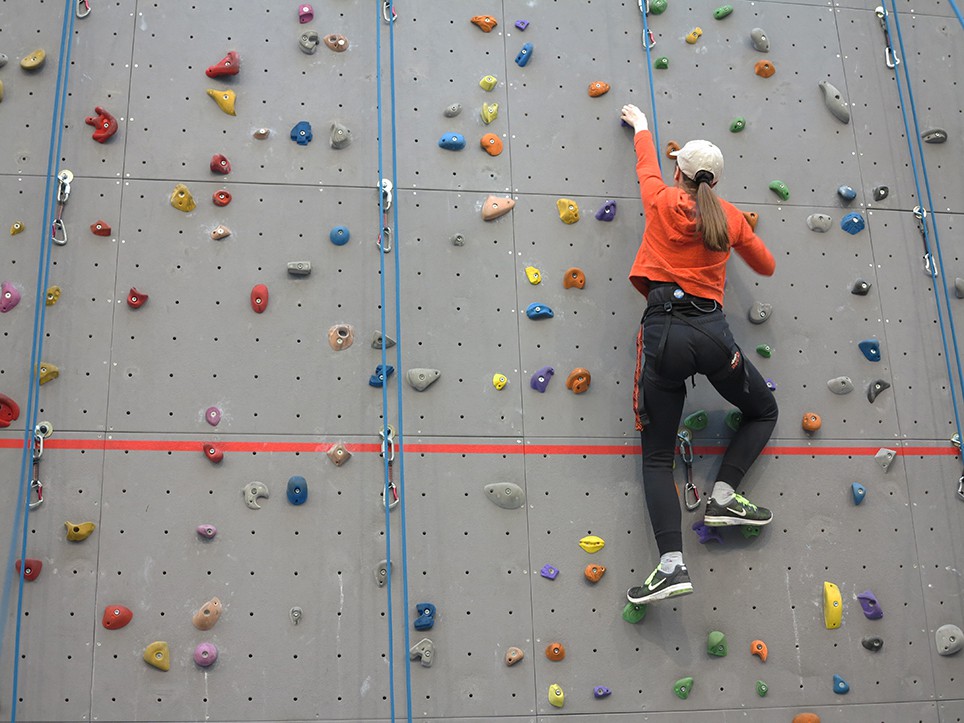
This Personal Protective Equipment (PPE) must comply with the applicable standards (Decree of 5 August 1994) and be regularly inspected (NF S72-701). Only PPE bearing the CE marking may be “(…) sold, rented or distributed free of charge (…)”.
You must therefore ensure that:
- all your equipment has a CE marking
- you organise the careful inspection of all equipment in service
- all non-compliant material is removed from service
standard NF S72-701:2008 concerns:
- the “Provision of personal protective equipment and safety materials for physical, sports, educational and leisure activities dedicated to the practice of climbing, mountaineering, caving and activities using similar techniques and equipment”.
- the procedures for the inspection and monitoring of PPE and similar equipment.
Our field experts are at your disposal for any quote.
Some safety equipment is not classified as PPE, so it is not concerned by this standard. However, the general safety obligation imposes the same rigor.
Identification and marking of the equipment
To allow individual or batch tracking, each material must be identified for traceability purposes.
In most situations, identification is achieved by marking the equipment.
- for ropes: according to the manufacturer’s recommendations, in general specific adhesive tape (be careful of tape solvents, which are not authorised), heat-shrinkable wraps, etc.
- for harnesses, quickdraws, straps, etc.: according to the manufacturer’s recommendations, in general, attached or sewn label, RFID chip
- for carabiners, mechanical equipment, etc: light engraving, paint, sticker, etc.
Any other identification process authorised by the manufacturer is possible. For example, the marking of ropes often ages badly when use is intensive: you can adopt another identification system, but no markers on the fibres!
material register
The standard specifies that the register of equipment must include all life records as well as manufacturers’ information and maintenance instructions.
The purchasing manager must therefore ensure that each information notice from the PPE is retrieved.
Be aware when the purchase relates to rope or cord sold by the meter, the seller must provide either the manufacturer’s documentation or the product references to find the documentation on the manufacturer’s website.
The requirements of the standard are cumulative with those of the manufacturer, and whichever is the most restrictive should be retained.
For example, the standard does not specify a lifetime limit for each PPE, however if a manufacturer, in its instructions for use, specifies a maximum lifespan / storage period, then that be must applied.
In case of computer monitoring, pending rules relating to electronic signatures, you will need to print a report for archiving at the end of each complete inspection signed by the inspector.
For each life record for item of PPE (or lot of PPE), the following should be recorded:
- type of equipment, manufacturer, model, identification
- date of acquisition
- year of manufacture
- date first put into use
- disposal deadline for equipment with a maximum lifespan
- user feedback
- possible changes in characteristics (length, condition of the rope, state of the harness: bridge, buckle, etc.)
- exceptional conditions of use that may compromise future use: shock following a fall of factor 2, wear of the rope on a sharp edge, etc.
- assessment of inspections according to the established timeframe
- a certificate of conformity of the equipment
Information for users
When provided with PPE, the user must:
- be informed of the conditions of use and maintenance of the equipment entrusted to them
- have the opportunity to consult the manufacturer’s instructions for use and the certificate of conformity
- be aware of the correct setting of the equipment
In the case of a supervised activity with provided equipment, it is up to the supervisor to:
- check the good condition of the equipment
- provide users with the necessary information about the hardware they use
- teach each user to systematically perform routine checks before starting the activity
When the equipment is returned, the supervisor or user must report any significant fall, any exceptional event or any defect found. This procedure can be formalised by signing a form or entering it into the PPE register.
Ppe inspection services offered by pyramide
- creation of a security register in accordance with the NF S72-701:2008 standard for monitoring
- individual labelling of each harness, strap, carabiner, rope, and other PPE
- entry of all PPE in the material tracking register
- careful control of all wear and safety points of each PPE
- immediate removal of all dangerous or obsolete PPE – they are then placed in a closed bag marked “discarded” and handed over to the owner
pyramide tips
- Keep PPE invoices and notices when purchasing
- Have the markings and inspections carried out by personnel with the required competence (certified) and legal protection (civil liability).